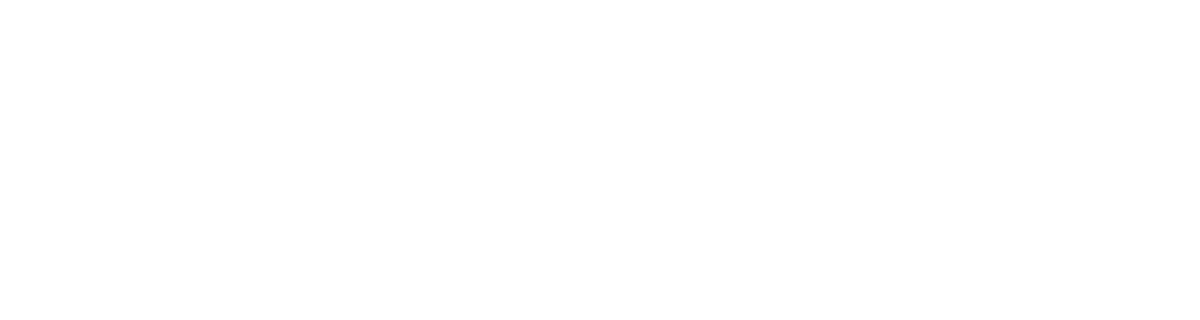
Mondelez is an international snack manufacturing organisation with in excess of 90,000 employees. In 2018 they engaged with Peko following a review of their current scheduling processes for the business-critical engineering team.
It was discovered that both employees & the unions were unhappy with the current distribution of opportunities for additional work. Also, the process for managing planned & unplanned absences was arduous for planning managers.
What was the challenge Mondelez was facing?
Peko worked closely with the Mondelez planning team to identify what the current process was for managing core resourcing & managing overtime opportunities. It became apparent that planning managers were overwhelmed with finding the right resource for the right opportunity & unconscious bias towards individuals was at work.
We found that in some cases there would be a doubling up on some shifts where a person had cancelled their holiday & the information had not been shared with the person covering that shift. This was costing Mondelez extra salary each month – eroding their operational profit.
How did Peko deliver radical change for Mondelez?
Engagement with all parties was critical to the success of the implementation process. The Peko team spent time with the unions, planning teams & users to ensure that they were all part of the change process. Defining the Mondelez business rules to ensure that the system was fair for all is a core part of the value proposition for Mondelez. The visibility of opportunities based on skills & resource requirements meant that Peko became the single source of truth for all.
Resourcing became demand-led & based on data that was visible for the planning teams. By having visibility of the resource availability vs production demands, Peko showed a saving of c 25% in overtime spend & produced ROI within 3 months of deployment.
Testimonial
“We needed a more efficient way to manage our engineers’ shifts, holidays, & overtime at Mondelez. Peko now approves holidays, & finds cover automatically based on rules we’ve set. It also makes sure each of our engineers have a chance at overtime opportunities.
Our managers now have more time to focus on strategies that bring more value to the business. This has resulted in significant ongoing savings to the business, along with more clarity & flexibility to our engineers.
The system also proved incredibly useful during the Covid-19 lockdown, to ensure the right people were on site.”
Kent W Ryley (Technical Lead), Mondelez International
People & Technology Working Together
Peko is based on the utilisation of a tried & tested fairness algorithm. By allowing Peko to manage the scheduling & ensure that there are no gaps in the resourcing the teams have been empowered to manage their time & work additional hours when they have availability.
Mondelez has seen this as a paradigm shift in how they plan & manage their people. Visibility, transparency & continuous improvement have allowed Mondelez to focus on quality & efficiency.
Mondelez has become agile in their production management & the employee interactive management tool has been transformational for the business.
Technology was introduced to empower our teams.